Quick connectors for brake vacuum lines despite higher temperature requirements in the engine room
The issue of CO2 reduction is still a hot topic. The aim is to achieve this by massive engine downsizing, weight reduction while increasing power. Better insulation of the engine compartment also reduces driving noise and thus provides a more pleasant driving experience. All these measures, however, increase the engine temperature and this requires new and higher performing materials.
This temperature increase is accompanied or even reinforced increased by the modified installation position of the turbo loader in order to achieve better emission levels. In the past, most components in the auxiliary units in the engine compartment were designed with continuous service temperatures of 120 °C and 1500 hours as well as peak temperatures of up to 150 °C. Recent engine developments, however, require continuous service temperatures of 160 °C over 3000 hours and peak temperatures of 190 or even 210 °C.
New generation quick connectors
AFT Automotive GmbH from Greven, North Rhine-Westphalia, was commissioned to develop quick connectors for brake vacuum lines that could withstand this temperature level. Particularly for components which need to be opened frequently, the above application entails a complex requirements profile as in addition to thermal ageing, they must also withstand high outer fibre stress without fracturing.
When seeking materials that withstand these enormous temperature loads, PPA and PPS grades were initially tested. Both polymers have excellent thermal ageing properties. They also meet the requirements for surface roughness of <RZ 6.3 in the seal area. However, the elongation at break of the component for the detachable connection of these quick connectors and the joint weld line strength did not suffice even before ageing.
Polyamides with heat stabilisers tested
After that, various polyamide 6.6/6 formulations were tested on the basis of new heat stabilisers (shielding technology), as they have both good joint weld line strength and a high elongation at break. 4 different polyamide compounds available on the market were examined. All 4 materials are able to fill the component geometry and the thin-walled area of the closing mechanism in particular (see figure 5). The PA 6.6/6 blends responded favourably, as they require less pressure when filling the cavities and as such can be processed at lower melt and mould temperatures. The heat ageing behaviour of the 4 materials was then examined. Tests were conducted as follows in order to determine the limits:
Each material was tested with the following temperatures in 3 cycles of 900 hours T 1 and 100 hours T2:
1) T1 = 120 °C T2 = 150 °C
2) T1 = 140 °C T2 = 170 °C
3) T1 = 160 °C T2 = 190 °C
As shown in figure 1, all materials showed increasing strength of the coupling latch after the first heat cycle at a lower temperature. This can be explained both by the declining tension in the injection moulding process and by the post-crystallisation of the materials. At the higher temperature, there were significant differences between the materials right from the first test cycle. Materials A, C and D (PA 6.6/6 GF 30) show the smallest decline, whereas material B (PA 6.6 GF 30) showed significant deterioration of the properties in the 160 °C and 190 °C interval after one third of the test duration.
After completing three cycles with the above temperature profile, material A, AKROMID® C3 GF 30 5 XTC (4499), an electrically neutral stabilised polyamide 6.6/6 with 30% glass-fibre reinforcement made by AKRO-PLASTIC GmbH, proved to be the best suited material. The connectors manufactured with this material show the same strength after 3000 hours as at the beginning. The greatest advantage is in the high elongation at break after ageing. This was the only tested material where the component was still able to be activated multiple times without fracturing after storage at maximum temperatures. In all the other materials tested, the lock rings broke after the ageing test. This is attributable not only to the excellent material properties, but to the CAD-optimised geometry of the opening mechanism.
Shielding effect
Innovative stabilisers now allow the manufacture of polyamides with thermal ageing behaviour which were only recently unthinkable. This stabilisation utilises what is known as a shielding effect (see figures 2 and 3). An effect whereby the stabiliser produces a kind of patina on the surface of the plastic component, which is almost impermeable to oxygen. This prevents further oxidisation of the material. This effect begins at an activation temperature, which varies according to the additives. In the case of XTC stabilisation of AKRO-PLASTIC, activation takes place between 170 and 180 °C. Another stabiliser protects the formulation up to this temperature, which means that the materials cover a temperature range of up to 230 °C. To safeguard different temperature ranges, the formulation was aged 3000 hours at 150 °C, 180 °C, 210 °C and 230 °C. The material was also aged with different intervals between 150 °C and 210 °C in order to prove that the stabilisation works under the different conceivable loads in everyday driving. The elongations at break after ageing shown in figure 4 show more particularly the potential of this new range. At all temperature variations, the residual elongation at break remains above 1.5% (dry), and after constant storage at 210° C it lies at a remarkable 2.7% after 3000 hours.
The mounting process at AFT for quick connectors (see figure 5) especially given the fact that the components are integrated in safety-relevant systems is conducted solely on fully automated systems. The components are then subjected to 100% leak test, monitored visually by camera system and the component-specific test results documented. Due to the possibility of remaining within the PA 6.6 material range despite the very high temperature requirements, it was not necessary to modify the assembly and testing process due to changed material requirements or design adjustments. As such, excellent process stability was achieved and ensured.
Both AFT Automotive and AKRO-PLASTIC work under the philosophy of guaranteeing optimum product quality at all times. Quality assurance testing is therefore conducted at every stage of production at both companies.
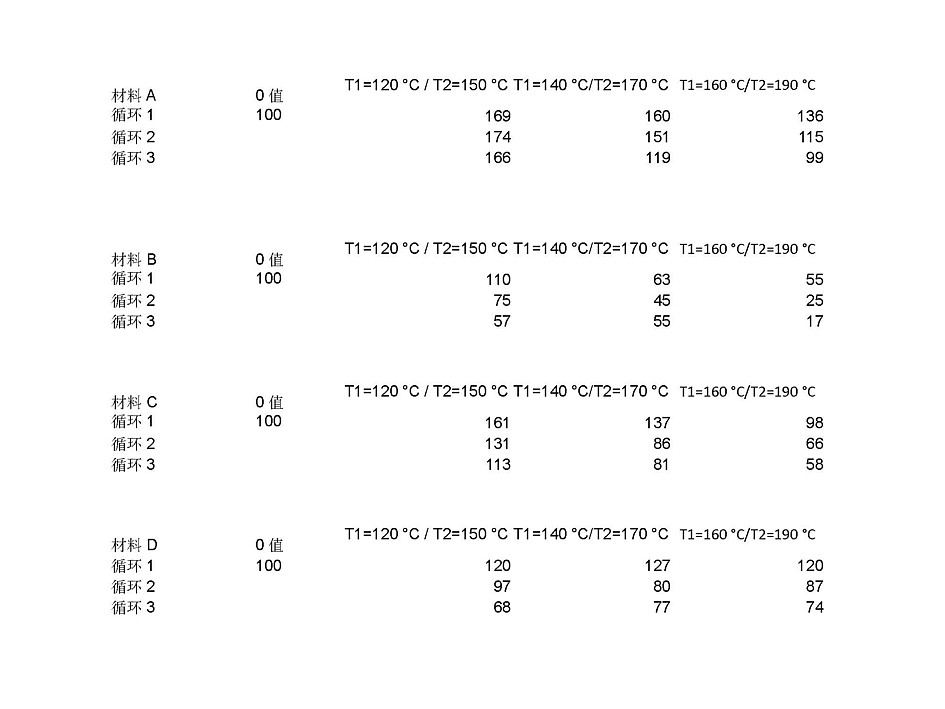
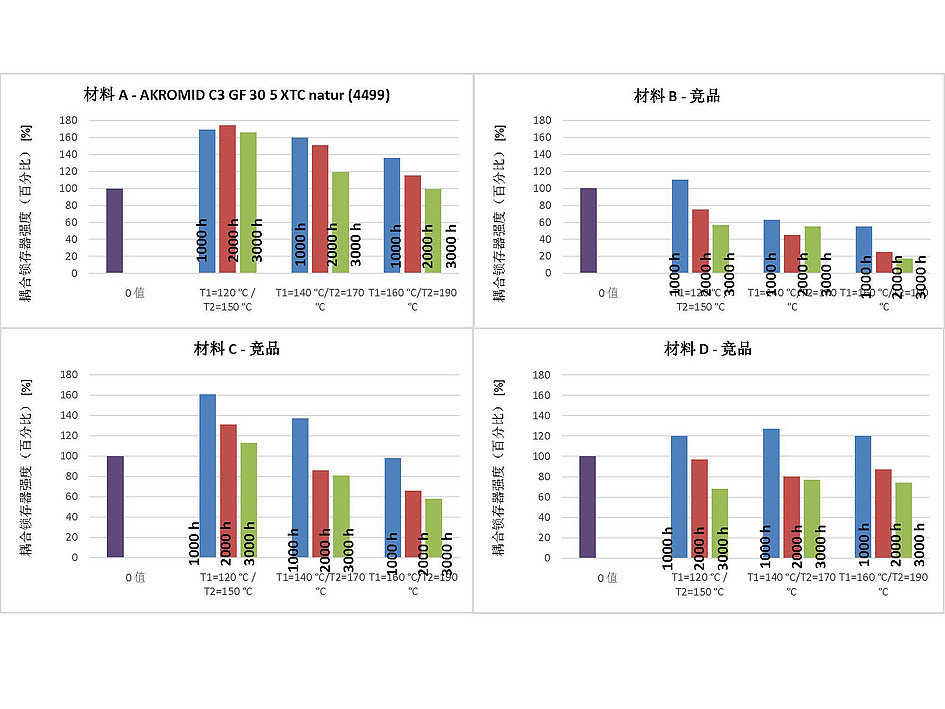
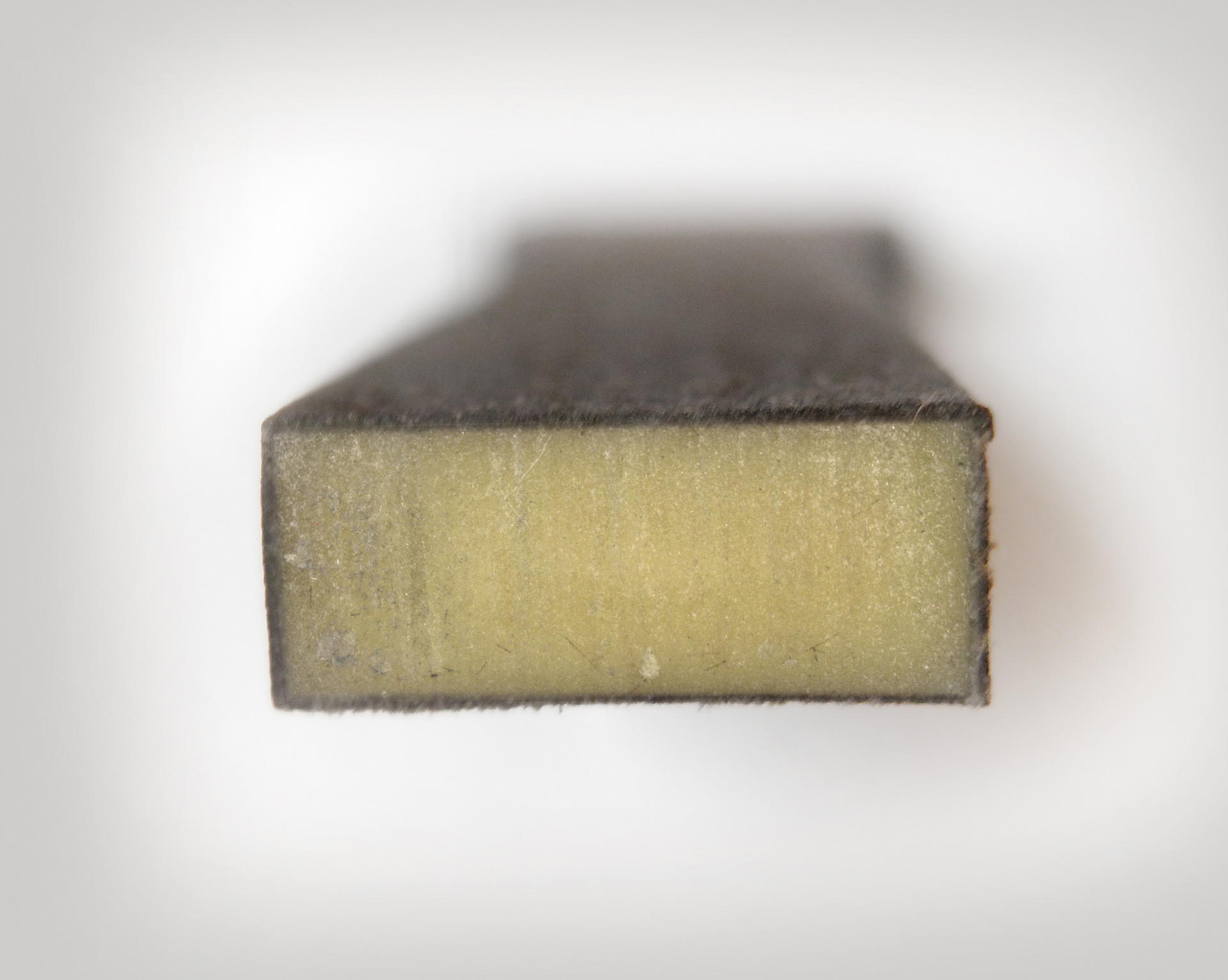
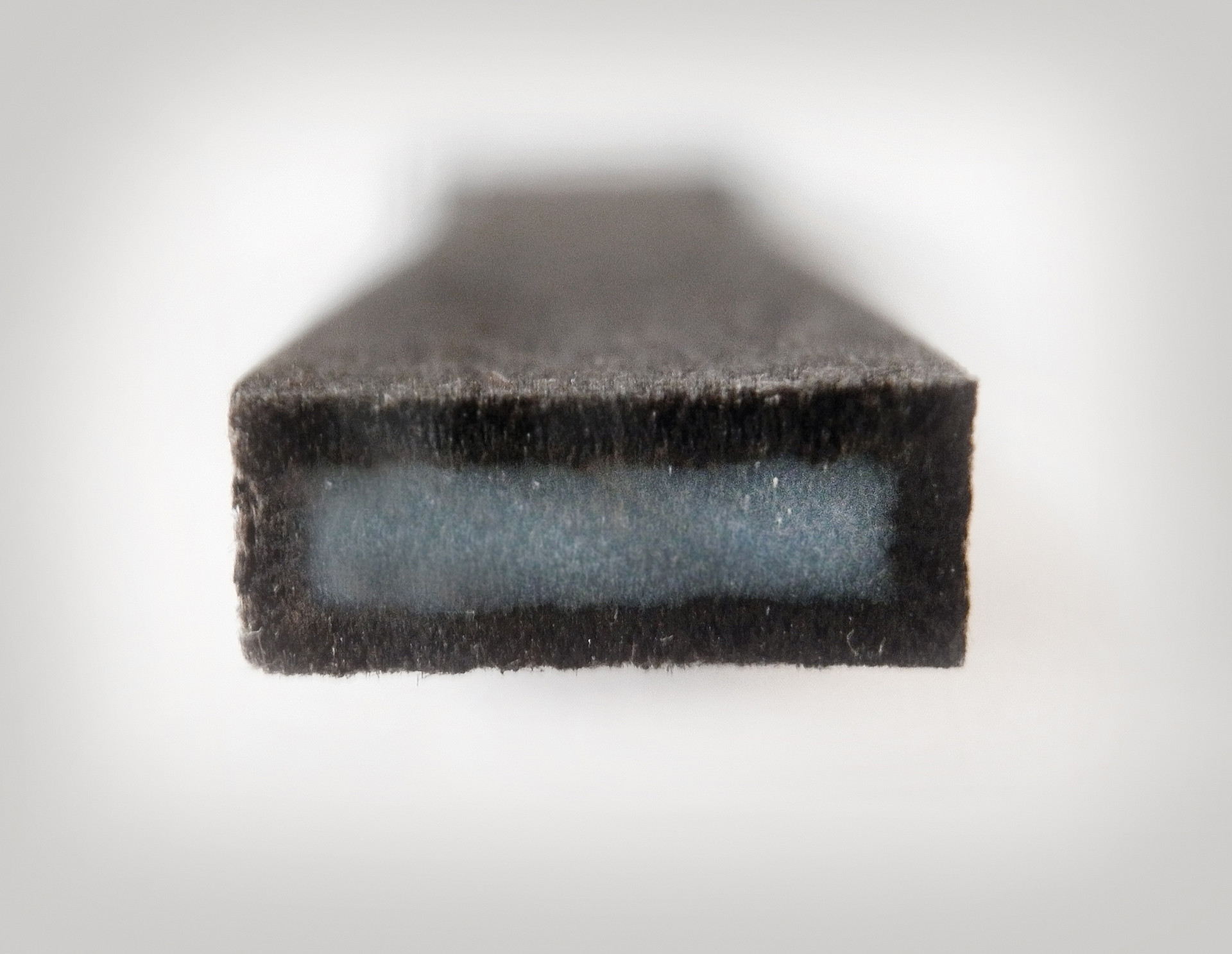
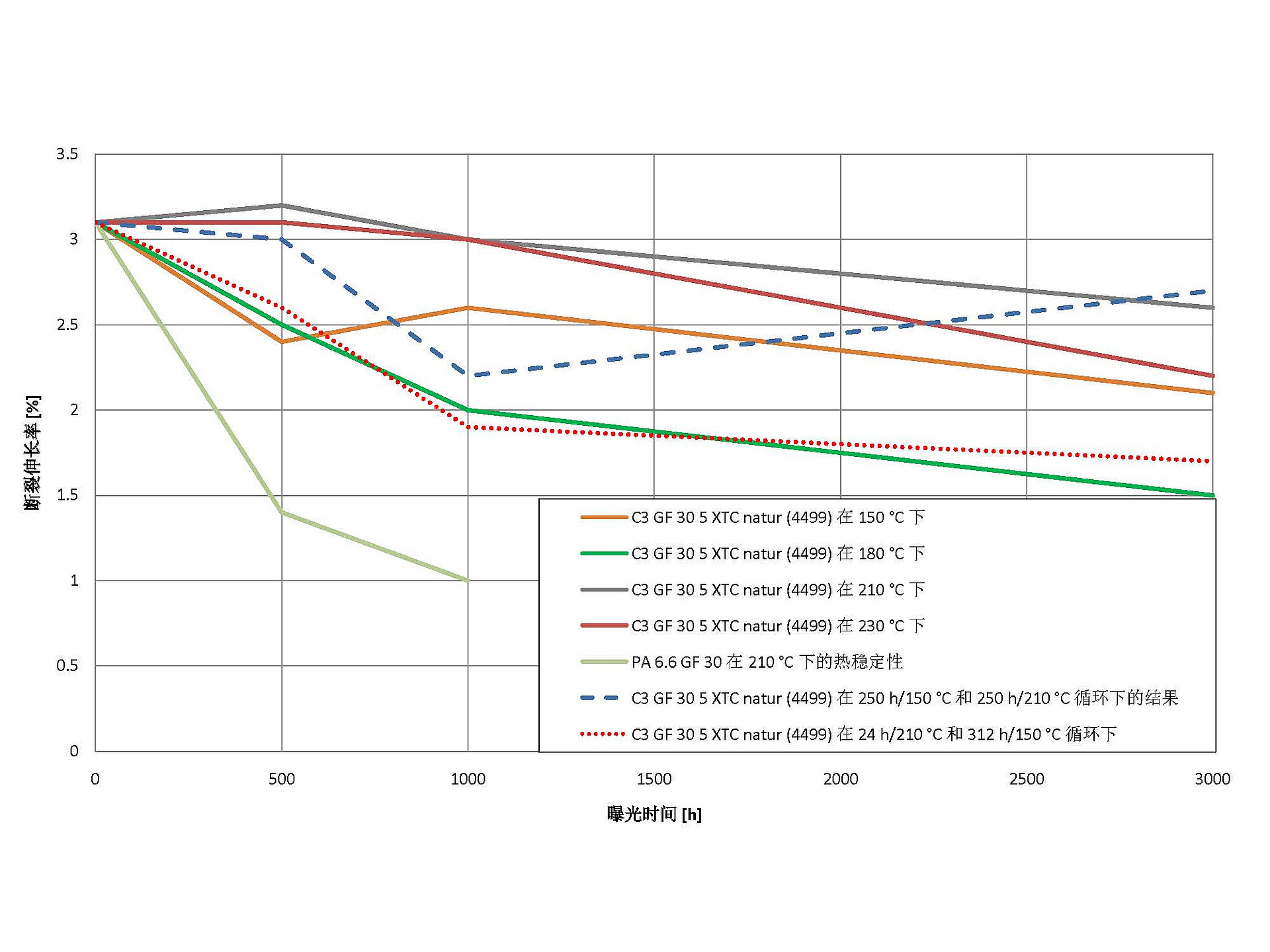
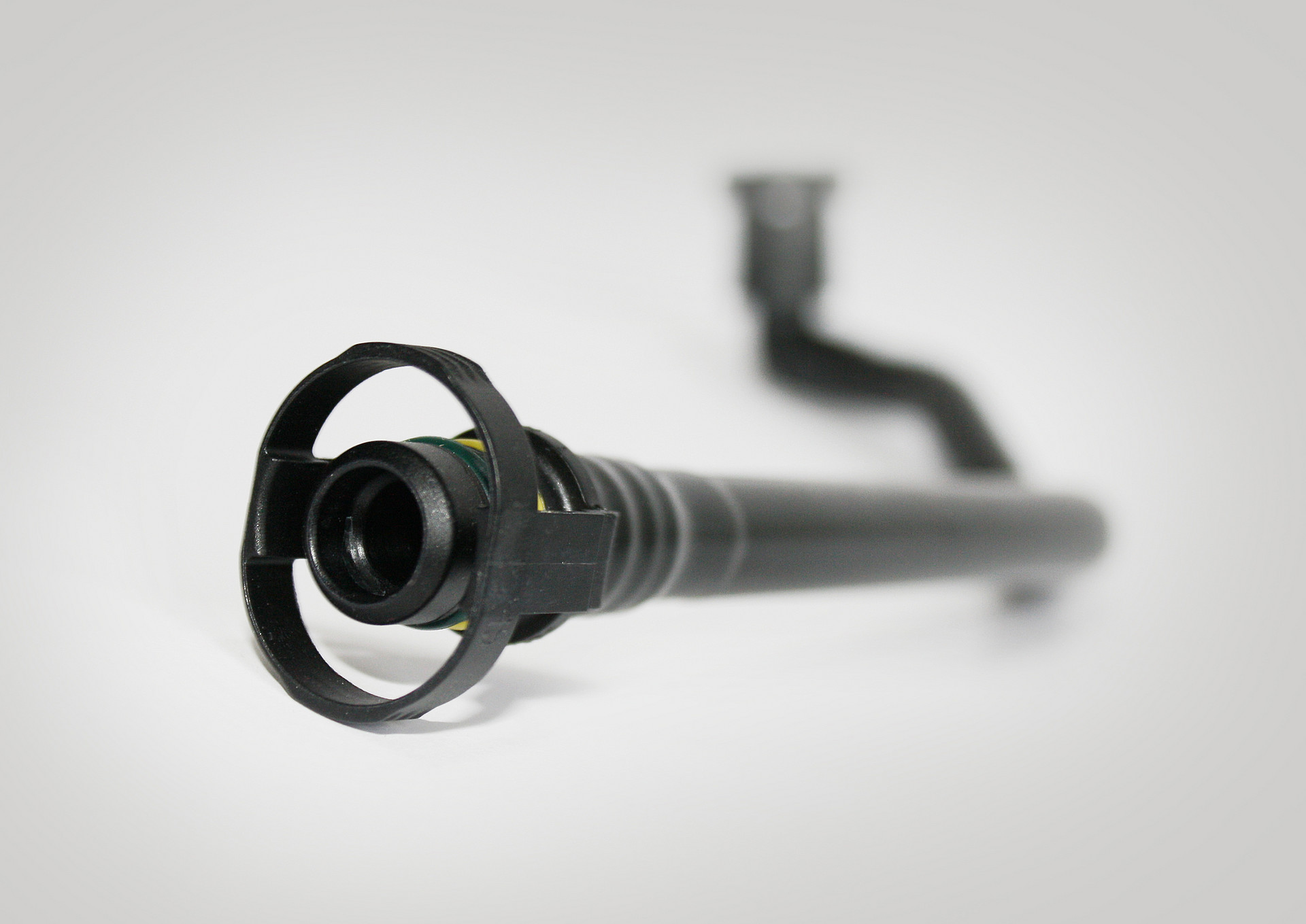
The authors:
Herman Cichorek is Head of Development at AFT Automotive GmbH, Greven
Dirk Kramer is the Managing Director of AFT Automotive GmbH, Greven
Thilo Stier is the Division Manager for Sales and Innovation at AKRO-PLASTIC GmbH, Niederzissen